2019年9月,华为公司在中国和德国同步发布麒麟990 5G芯片,也是全球首款将5G Modem集成到SoC(System on Chip,系统级芯片)上,当时其板级面积相比业界其他方案小36%,称为业界最小的5G手机芯片方案,并且内含103亿个晶体管,是世界上第一款晶体管数量超过100亿的移动终端芯片。麒麟990 5G无需额外添加外挂5G芯片就能实现5G网络。华为麒麟990 5G芯片的设计领先全球,并且采用的加工工艺也是目前精度最高、技术最先进的7nm+EUV光刻工艺(Extreme Ultraviolet Lithography,极紫外光刻),当时是交给台湾积体电路制造股份有限公司(台积电)代加工生产。除了华为,CPU(Central Processing Unit,中央处理器)领域的巨头AMD也是交给台积电代加工生产。由此可见光刻工艺的技术难度极高。
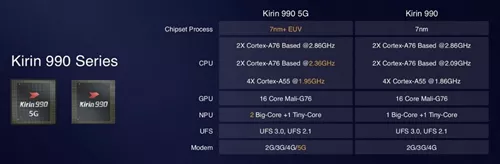
华为麒麟990 5G 芯片
光刻技术的高低直接决定集成电路芯片的质量高低,所谓光刻技术就是借助光致抗蚀剂(光刻胶),在特定光源照射下进行曝光,然后经过显影、刻蚀等步骤,将掩模版上预先设计好的图案转移到衬底晶圆上的技术。一款性能优异集成电路芯片的诞生不仅需要设计创新,同时也需要具备先进光刻技术。我国具备优异的自行设计多功能芯片的能力,但是非常受限于生产芯片的光刻技术。光刻技术包含光源、光刻胶以及光刻工艺三个核心要素,其中光刻胶是光刻过程中最关键的功能材料。光刻胶是一种光敏感材料,曝光过程中(紫外线照射等)会发生某些化学反应,使得曝光区域在显影液中的溶解性发生变化,然后经过显影液显影之后得到特定的由元器件以及电路组成的光刻图案。光刻胶主要由成膜树脂、光敏物质、溶剂、适当的助剂四部分组成。其中,成膜树脂是光刻胶的主要成分,对整个光刻胶起到支撑作用,使光刻胶具有耐刻蚀性能,对光刻胶的性能有重要影响。

正性胶与负性胶的光刻显影工艺
光刻胶的制备方法复杂,品种繁多。依据光刻胶在曝光前后在显影液中的溶解性差异可以将其分成两类:正性光刻胶和负性光刻胶。正性光刻胶在曝光区域发生的化学反应能导致其在显影液中的溶解性增强,显影之后遗留的掩模版遮掩区域为设计的芯片图案;反之,负性光刻胶在曝光区域发生的化学反应能降低其在显影液中的溶解性,而掩模版遮掩区域反而可溶于显影液,从而获得和掩模版互补的芯片图案。
光刻胶的关键性能指标
英特尔(Intel)创始人之一戈登·摩尔(Gordon Moore)总结出摩尔定律,其核心内容为:集成电路中可容纳的晶体管数量每经过18~24个月总数增长一倍,换言之,含集成电路的处理器性能每隔两年翻一倍。到目前为止,半导体器件的发展趋势都沿续了摩尔定律的规则,并在其推动下,光刻技术也在不断发展。集成电路也逐渐向大规模甚至超大规模发展,芯片加工工艺越来越严苛,对于光刻胶性能指标也逐渐升高。
1. 分辨率
在特定设备以及光刻工艺条件下,光刻胶能达到的最小分辨率,这直接决定芯片的集成度以及运算速度。
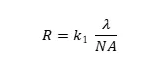
光刻胶的分辨率R和曝光波长λ(nm)成正比,和镜头的数值孔径NA(小孔成像原理)成反比,K1为工艺系数。保持其他参数不变的情况下,降低曝光波长可以有效提高光刻胶的分辨率。光刻技术也从初始的宽谱曝光、紫外G线(436 nm)、H线(405 nm)、I线(365 nm)一步步降低至深紫外(248 nm KrF、193 nm ArF、157 nm F2)、极紫外(13.4 nm),继续开发出了X射线光刻、电子束光刻、离子束光刻等光刻工艺。随着光刻工艺的不断提高,所需光刻胶相对应的成膜树脂性能要求不断提高。
2. 敏感度
光刻胶在曝光过程中(紫外光照射)发生化学反应导致溶解性发生变化,从而获得高质量图案所需要的最低能量(最小曝光值),单位为mJ/cm2,不同类型的光刻胶具有不同的最小曝光值。敏感度越大,单位时间内芯片的产出越高。然后,过快的敏感度对工艺的稳定性有所影响。
3.工艺窗口
工艺窗口即光刻胶性能,尤其是线宽受工艺波动的影响,光刻胶线宽受曝光能量变化的影响称之为“曝光宽容度(Exposure Latitide, EL”;光刻胶线宽受焦距变化的影响称为“焦深(Depth of Focus, DoF)”。
4. 抗刻蚀能力
光刻胶对光刻工艺之后的其他工艺的阻挡能力称之为抗刻蚀能力,具体表现在耐热性(在高温下不发生形变)、抗刻蚀性(在刻蚀过程中,光刻胶的损失较小,有较大的刻蚀选择比)、抗离子注入能力(在一定厚度下对离子注入的抵抗,确保不被所注入的离子击穿的能力)等。
光刻胶的发展历程
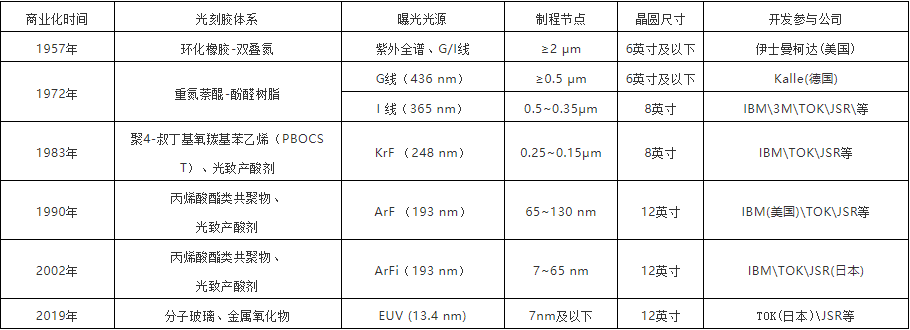
光刻胶的发展历程
1. 光刻胶的先驱:柯达KTRF光刻胶
1950s美国柯达公司首先开发了聚乙烯肉桂酸树脂光刻胶,商品命名为KPR,但是该材料对硅片的附着力不够,材料的表面粘附性较差,涂膜不均匀,显影时容易出现胶膜溶胀等缺陷。柯达转而寻找具备强附着力的材料,并最终开发出环化橡胶-双叠氮体系,柯达将此光刻胶命名为 Kodak Thin Film Resist(柯达薄膜抗蚀剂),也即 KTFR 光刻胶。基于KTFR的光刻胶一般采用重氮萘醌为感光剂,感光剂曝光后失去氮产生硝酸,引发副反应,曝光部分在显影液中不溶,由于易发生膨胀导致周边出现毛刺,使其分辨率受到限制,因此该类光刻胶的分辨率极限在2μm。该体系在1957~1972年间一直为半导体工业的主力体系,为半导体工业的发展立下了汗马功劳。

KTRF光刻胶
2. G线/I线光刻胶
随着光刻设备进一步提升,曝光波长进一步缩短,光刻胶厂商开始再次寻找分辨率更高的新一代光刻胶材料。当曝光光源发展到G 线(436 nm)和I 线(365nm)等单波长光源,贝尔实验室和Azoplate公司在一次意外尝试中发现酚醛树脂-重氮萘醌具备优异的抗刻蚀性能,为正型光刻胶,由线性酚醛树脂作为成膜树脂,重氮萘醌为感光剂,商业化命名为“AZ光刻胶”。G线光刻胶主要适用于0.5~0.6 μm集成电路的制作,而I 线光刻胶主要适用于0.35~0.5 μm集成电路的制作。现今在High-NA技术的I线光源支撑下,AZ光刻胶的分辨率极限已经可以达到0.25 μm。
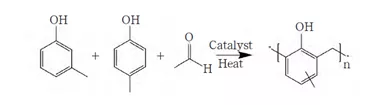
酚醛树脂合成
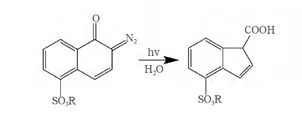
重氮萘醌感光机理
3. 化学放大光刻胶
20 世纪 80 年代,深紫外(DUV)光刻系统开始逐步投入使用,随着光刻系统所用波长的逐步降低,光源强度逐步成为制约生产效率的瓶颈,一方面是开发高功率光源,另一个方面是提高光刻胶的感光灵敏度,最终有效解决了这一问题的是化学放大型光刻胶。化学放大型光刻胶包括成膜树脂、光致产酸剂、添加剂以及溶剂4个主要组成部分。其作用机理是光致产酸剂吸收光产生酸,酸催成膜树脂发生脱保护反应,实现树脂由不溶于显影液转变成可溶于显影液。这一过程中,酸作为催化剂,不会被消耗,因此可以将光的信号放大为化学信号,这也是这一类光刻胶称为化学放大型光刻胶的原因。化学放大型光刻胶的光利用效率远高于传统的感光化合物基光刻胶。化学放大法是几乎所有现代光刻胶成功的关键因素。
3.1. KrF(248 nm)光刻胶
当光源由365 nm缩短至248 nm时,一直在365 nm有较好光刻效果的酚醛树脂在248 nm有较大吸收,不利于形成垂直的形貌,同时由于KrF 248 nm光源强度较弱,急需开发具有较好感光性的光刻胶。IBM公司率先研发了适用于248 nm光刻工艺的聚对羟基苯乙烯(PHOST)。聚对羟基苯乙烯是一种苯乙烯基聚合物,在分子骨架上加入一个叔丁氧羰基(tBOC)侧链保护羟基,从而获得新的聚合物PBOCST。PBOCST光刻胶暴露在248nm深紫外光下时,PAG产生的酸会打开 tBOC保护基团,光刻胶溶解性发生显著变化。打开 tBOC的过程中,PAG 产生的酸并不会被消耗,因此PBOCST光刻胶反应速度极快,对深紫外光非常敏感,灵敏度提高了100~200倍,光刻工艺分辨率可以达到0.25~0.3 μm,直接逼近I线(365 nm)的光刻极限。
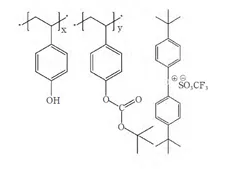
248 nm光刻胶成膜树脂和光致产酸剂
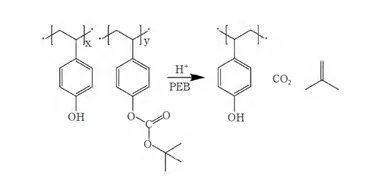
化学放大型光刻胶反应机理
3.2. ArF(193 nm)光刻胶
当集成电路制造工艺发展到90nm节点时,原本用于KrF光刻体系的PBOCST 光刻胶在193nm的波长下会表现出强烈的吸收,不能满足新的光刻要求。193 nm深紫外光刻技术的曝光光源为ArF准分子激光器,适用的成膜树脂需具备(1)较高的光学透明性,在193 nm处具有低吸收;(2)较高的抗刻蚀能力;(3)具有酸敏感基团,适用化学增幅技术。ArF(193nm)光刻胶逐步发展为主流光刻胶,发展前后主要分为两个方向:干法ArF光刻胶和沉浸式ArF光刻胶。对于193 nm波长,常用的为丙烯酸酯类树脂,并且通过不同单体的共聚可以实现对树脂性能的控制。现阶段沉浸式ArF光刻胶在双重图形/多重图形曝光技术的支持下,工艺节点分辨率已经可以达到至7~10nm。
4. 下一代光刻技术:极紫外(EUV)
极紫外光刻是利用波长为13.5 nm的极紫外光进行曝光的一种方式,由于波长短,这一曝光方式具有优异的分辨率。随着线宽的不断减小,EUV光刻胶必将面临RLS(分辨率、边缘粗糙度、光敏度)的挑战。即在光刻胶的分辨率(R)、边缘粗糙度(LER)和光敏性(S)3者之间只能实现2个参数的最优化,随着线宽的不断减小,LER对图形的影响越来越大。降低LER的有效策略主要包括:(1)增加碱性添加剂;(2)在树脂上通过化学键连接光致产酸剂(PAG);(3)分子玻璃光刻胶;(4)基于金属氧化物的光刻胶。上述的4个方法中,增加碱性添加剂主要是为了控制酸的扩散,但是增加碱性添加剂后需要更大的曝光能量,也就是损失了光刻胶的光敏性。将PAG键合到树脂上,可以实现对酸扩散的精确控制,但是大部分的研究只是将阳离子固定在树脂上,曝光后生成的酸是游离的,这样并没有太大的作用,而将阴离子固定在树脂上,制备过程比较困难。策略(3)和(4),也就是分子玻璃光刻胶的研究与金属氧化物光刻胶是比较有前景的EUV光刻胶技术。分子玻璃是一种具有较高玻璃化转变温度的单分散小分子有机化合物,其结构为非共面和不规则,能够避免结晶,与产酸剂具有优良的相容性。以分子玻璃为成膜树脂制备的光刻胶能够获得较高的分辨率和较低粗糙度的图形。常见的分子玻璃体系主要为支化型或者树枝状型分子。
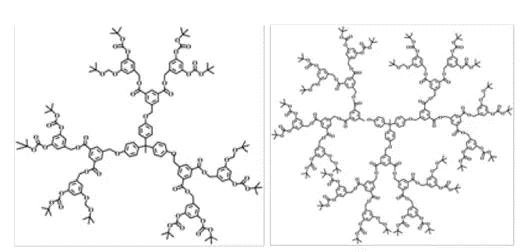
典型的树枝状光刻胶
金属氧化物光刻胶使用金属离子及有机配体构建其主体结构,有机配体中包含光敏基团,借助光敏基团的感光及其引发的后续反应实现光刻胶所需的性能。从化学组成来看,金属氧化物光刻胶主要为稀土和过渡金属有机化合物。
总结与展望
全球EUV光刻技术的研发始于20世纪80年代,经过近40年的发展,EUV技术从原理到零部件再到原材料等已经足够成熟。2019年5月,台积电宣布量产7 nm N7+工艺,这是台积电第一次、也是行业第一次量产EUV极紫外光刻技术,这其中开篇提及的华为麒麟 990 5G芯片就是采用这个加工工艺。2020年2月20日,三星宣布其首条基于极紫外光刻(EUV)技术的半导体生产线开始大规模量产,同年3月,宣布开始投建 5 nm EUV生产线。同时台积电也宣布其5 nm光刻工艺在2020年第二季度量产。
电子电器行业飞速发展,促使集成电路不断向高集成和高速化发展,对光刻技术的要求越来越高。国际上实现应用的最先进的光刻技术为EUV光刻,相对用的功能材料光刻胶成为电子化学品中技术难度最高的材料之一。我国对其研究开发起步较晚,不论在光刻胶下游的IC制造还是与其搭配的光刻机方面,均与全球顶尖水平存在差距。再加上发达国家一直将光刻胶作为战略物资加以控制,导致我国在相关领域当前仍处于追赶阶段。高端的光刻胶产品受到发达国家管制,我国目前只能生产低附加值的中低端产品。我国必须加快加深对光刻技术及相关材料的基础研究,实现EUV光刻技术及其关键材料的突破,争取在EUV光刻领域中缩小与国际先进水平的差距。
参考文献:
1. 光刻材料发展状况及下一代光刻技术对图形化材料的挑战,新材料产业,2018, 12, 43-47.
2. 光刻胶发展概述,信息记录材料, 2015, 16, 42-49.
3. 电子束光刻胶成膜树脂研究进展,信息记录材料,2016, 17, 1-8.
4. 光刻胶及其成膜树脂的研究现状,广东化工,2020, 47, 76-77.
5. 信心光刻技术研究进展,激光技术,2019, 43, 30-37.